New version of the TCG 2032 added to the product line
Seven questions on the new TCG 2032 gas engine put to Melf Thomsen, product manager at MWM
MWM Newsflash: After two years of concerted continuing development work, the new version of the TCG 2032 gas engine was recently introduced. Mr. Thompson, what are the main product features that will be important to customers?
Melf Thomsen:
We achieved three big advances that will matter to customers: Efficiency, ability to operate in island mode, and maintenance intervals. The electrical efficiency of the genset is now as high as 44.1%, which permits an output of 3333 to 4300 kW el. Based on the excellent experience we have already had with previous versions, we were able to increase the service interval for major overhauls from 64,000 to 80,000 operating hours.
MWM Newsflash: How is MWM meeting market needs with this development?
Melf Thomsen:
The main customer requirement at the beginning of the project was to improve the load response capability of the power generators and simultaneously increase the electrical efficiency at full load. This led to the engineering task of increasing the reserve boost pressure of the turbocharger at partial loads in order to make it possible to add and shed larger loads than before. The losses at the throttle valve in continuous operation at 4300 kW el had to be reduced in order to achieve higher efficiency. At the same time, the units needed to have sufficient reserve at full load to handle short-term fluctuations in temperature and gas quality without a change in output.
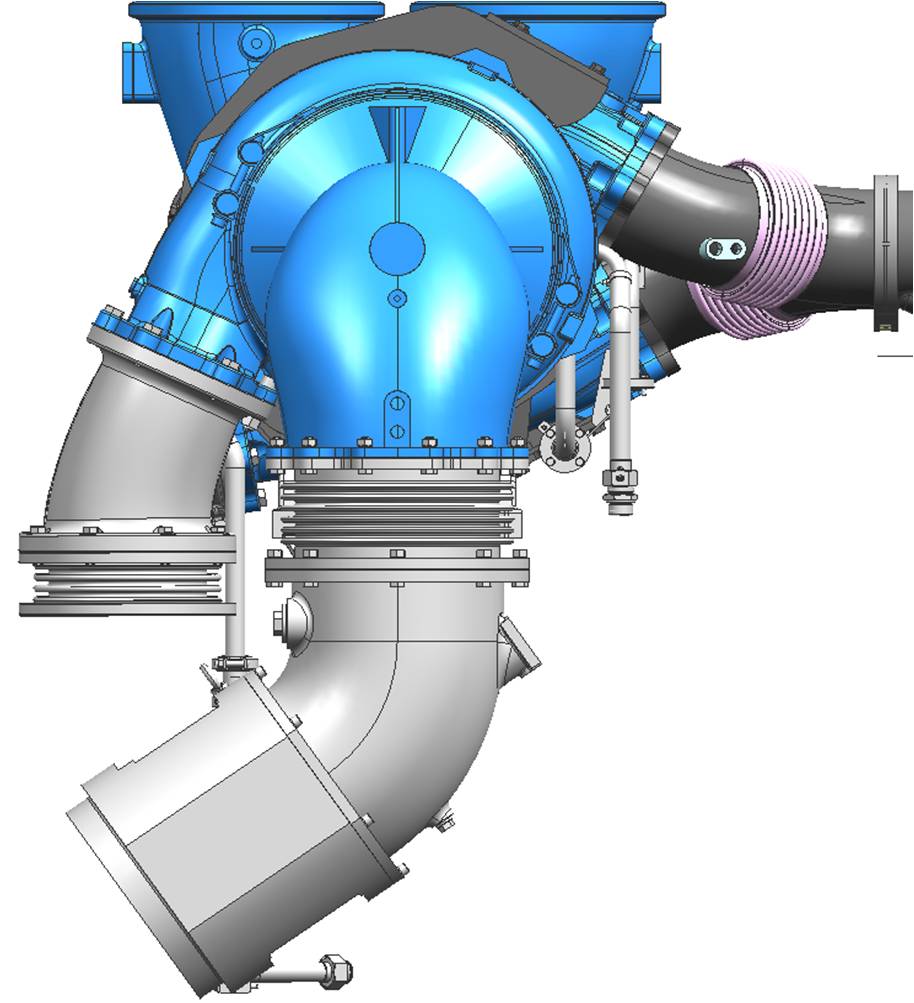
MWM Newsflash: How did you achieve this goal?
Melf Thomsen:
From these requirements we determined that three main measures were needed: Modification of the turbocharger, modification of the geometry of the MWM pre-chamber spark plugs and the introduction of a multivariable controller. This controller simultaneously manages actuators found on the gas engine, such as the throttle valve, gas mixer and wastegate.
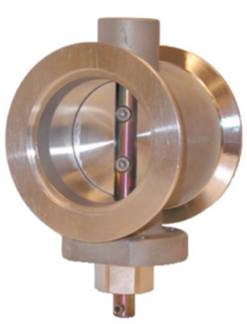
MWM Newsflash: Can you explain these measures in detail?
Melf Thomsen:
The two turbochargers that are installed as standard equipment on the TCG 2032 V12 and V16 engines were equipped with a new exhaust gas turbine. Based on the increases in efficiency on the exhaust gas side, a higher boost pressure is automatically provided on the compressor side of the turbocharger. This higher boost pressure becomes particularly advantageous in the partial-load range in adding or shedding electrical loads. In addition to the turbochargers, the MWM pre-chamber spark plug, already a proven feature of MWM engines, was modified. This pre-chamber principle achieves higher efficiency and simultaneously reduces maintenance costs and makes for simpler peripheral equipment. The modified spark plug geometry accelerates and stabilizes combustion in the TCG 2032 gas engine. This results in an improved utilization of the gas-air mixture in the combustion chamber, which makes the engine more efficient.
MWM Newsflash: What role does the TEM controller play in the new TCG 2032?
Melf Thomsen:
Probably the most important change in the new version of the TCG 2032 gas engine is the introduction of a new controller, which combines the individual controllers that were previously used on the engine. In the past, the actuators on the engine were accessed by various controllers for engine output, rpm, emissions and boost pressure (each separately from the other). When electrical loads were added to the unit, the throttle valve was first opened completely, then the gas mixer was adjusted, and then the waste gate was closed after a bit of delay. When these control functions are combined in a multivariable controller, all of the actuators are addressed by a single controller, so that they immediately work together in order to meet the needs of the given situation. With this approach, it was possible to increase the individual load levels. So now only nine load levels are needed up to full load.
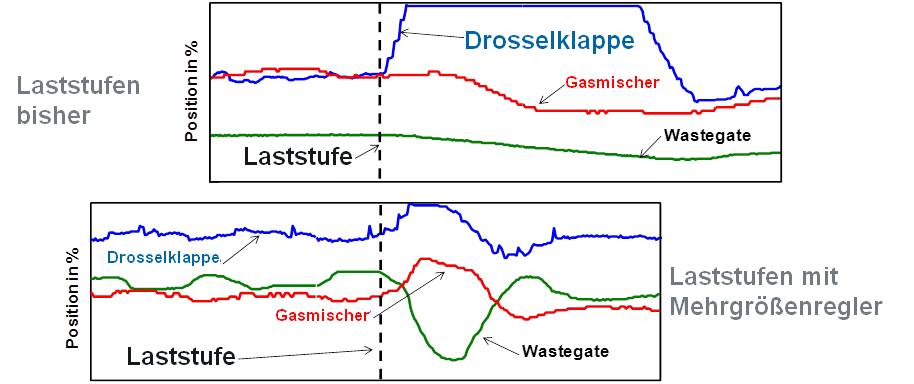
MWM Newsflash: How much of an impact have these measures had on efficiency?
Melf Thomsen:
The use of the new spark plug and the combined use of the new wastegate and throttle valve also make it possible to achieve the required increase in efficiency of the genset at full load. Now, at full load, the throttle valve on the gas engine can be opened further in order to reduce throttle losses. At the same time, the control reserve for fluctuating operating conditions is reliably provided by the wastegate. The increase in efficiency resulting from these measures is 0.7% absolute in the TCG 2032 series. As a result, the power generators now achieve an electrical efficiency of up to 44.1%.
MWM Newsflash: How do these measures affect the operating costs in plants?
Melf Thomsen:
In addition to fuel costs, which can be lowered substantially as a result of the efficiency of these engines, service costs also have a decisive impact on the magnitude of operating costs of cogeneration plants. Short downtimes during service work and, as a result, high availabilities continue to be ensured by our simple service concept, which utilizes exchangeable cylinder units and a small number of individual components. Regularly scheduled maintenance only occurs every 4000 hours (no more than twice a year). In the past, a major overhaul of the genset was necessary after 64,000 hours, which roughly corresponds to eight years of continuous operation. Based on our cumulative experience and the evaluation of numerous operating data, the time until a major overhaul is necessary can now be increased to 80,000 hours. In this way, service costs within the first 10 years can be reduced by more than 30%.
MWM Newsflash: Thank you, Mr. Thomsen.
Name: Melf Thomsen
Position: Product manager
With MWM since: June 2010
Stations: Daimler AG