MWM Answers – Economic Benefits from the Use of Internal Cogeneration Power Plants: From What Size Does It Pay for Medium-Sized Commercial and Industrial Enterprises to Run Their Own Cogeneration Plants?
Mannheim, 17.03.2020
The construction material, chemicals, glass, nonferrous metals, paper, and steel industries are positioned at the starting point of the value chain. These energy-intensive industries thus play a key role. However, the production processes of construction material and basic chemicals consume a lot of energy, which, besides labor expenses, represent one of the main cost factors in the energy-intensive industries. What is more, Germany’s power prices contain higher charges and levies than the EU average. Therefore, alternative energy solutions are necessary in order to sustain the international competitiveness of Germany’s energy-intensive industry.
Every year, Germany’s energy-intensive industries generate revenue of about €330 billion, some 18 percent of the revenue of the entire manufacturing industry. They invest more than €10 billion a year in their location in Germany and spend more than €17 billion on energy.
Producing and Using Power Heat and Power Directly in the Company
Cogeneration power plants enable flexible distributed power and heat generation in energy-intensive medium-sized enterprises. Fossil energy sources with a low environmental impact, such as natural gas or other special gases, can be used to fuel these plants. The cogeneration power plants convert the energy into heat and power. The heat is used at the cogeneration power plant site to heat the buildings, while the power is used for operating the manufacturing facilities.
In addition to enhanced energy security and optimization of production processes, internal power generation affords operators of CHP plants the opportunity to significantly cut operating costs and reduce their carbon output for a sustainable footprint. Cogeneration enables the distributed generation of power and heat right where they are needed. In contrast to separate generation, CHP plants lose far less energy in the generation process. This makes cogeneration a sustainable alternative. In view of their mode of operation, efficiency, and structural properties, cogeneration power plants in an output range of 400 to 10,300 kWel are especially attractive for medium-sized companies and organizations. In addition to the production and supply of power for the internal demand, part of the generated power can be fed into the power grid. Besides medium-sized industrial companies and retailers, cogeneration power plants can also be deployed in public swimming pools and government authorities.
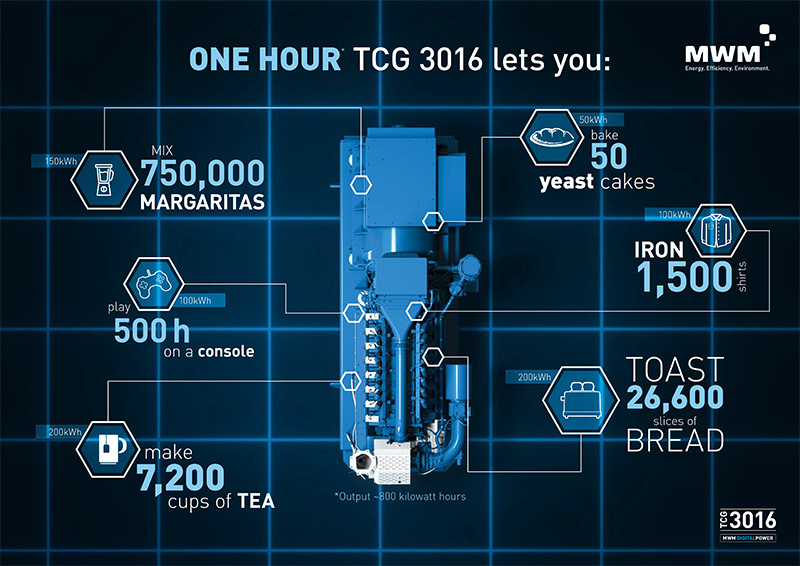
Cogeneration for Improved Efficiency
Compared to the separate generation of electrical energy and heat, combined heat and power (CHP) plants make better use of the primary energy. MWM cogeneration power plants enable economic, efficient energy generation. The employed energy is transformed into electrical energy and heat by the technical systems on site. The resulting exhaust heat can be reused directly and is not lost.
Cogeneration power plants can run on various fuels. Since the German Renewable Energies Act (EEG) entered into force in 2012, biogas-fueled plants have benefitted from special subsidization measures. To encourage operators to switch to flexible, demand-oriented power generation, the EEG 2017 offers a reliable perspective in the form of an optional feed-in tariff extension by up to 10 years including guaranteed power feed-in tariff.
Energy Independence with Internal Flexible Cogeneration Power Plant
The higher the electricity prices, the more economic an internal cogeneration power plant gets for the plant operators. Through the installation of heat storage units and flexibilization of the CHP plant, it is also possible to buffer any fluctuations in the demand for energy.
With its fees, charges, and levies, the electricity price for non-subsidized industrial enterprises in Germany is among the highest in Europe. For energy-intensive operations that do not get their power from internal power plants, the average electricity price in 2018 was about 84 percent higher than in 1998 and 184 percent higher than in 2000. This means a high financial burden particularly for energy-intensive medium-sized enterprises, e.g. in the construction materials, chemicals, paper, and steel industry.
By switching to distributed energy generation and flexibilization of their internal CHP plant, operators can save heat and power costs on a long-term basis. MWM’s highly efficient gas-fired CHP plants enable the implementation of modern, custom-tailored power plant solutions for sustainable and affordable distributed energy supply, which are especially suitable for the needs of energy-intensive operations.
For example, contact lens manufacturer Bausch + Lomb is able to cover 65 percent of its electricity demand and 91 percent of its heat demand with its internal MWM TCG 2032 V12 power genset. Thanks to the high plant availability of almost 98 percent and the outstanding reliability and efficiency of the MWM gas engine, the operating costs of Bausch + Lomb have dropped by up to €1 million a year.
Cogeneration Power Plants: Optimized Operation, Lower Production Costs, and Security of Supply in a Bundle
A significant reduction of the energy costs is not the only benefit of running an internal cogeneration power plant within the scope of the operations. An internal cogeneration power plant ensures security of supply especially for hospitals, hotels, administration buildings, the food industry, and the electrical industry, which depend on continuous, steady power supply. A year has 8,760 hours; for a cogeneration power plant to be profitable, it should operate for at least 5,000 hours a year.
The chocolate manufacturer Weinrich, for instance, needs ongoing cooling in the production process. The factory’s new energy center—which has an integrated natural gas-fueled MWM TCG 2016 V16 gas engine—bundles the generation of power, hot water, warm water, and cold water in a trigeneration plant. As a result of the modernization, the chocolate manufacturer is now able to cover two thirds of its power demand from its internal production with the MWM gas engine and the new cogeneration plant
CHP Success Stories: Efficiency and Sustainability as the Concept for Tomorrow
In this age of renewable energies, the need for sustainable power generation is on the rise. By switching to energy-efficient, eco-friendly production, the chocolate manufacturer Weinrich saves both energy costs and up to 1,950 t of carbon a year.
For MWM, sustainability means long-term economic efficiency along with modest use of resources. MWM offers an extensive range of gas engines, power gensets, and turnkey CHP plants that meet highest quality requirements as well as international pollution and fuel consumption standards.
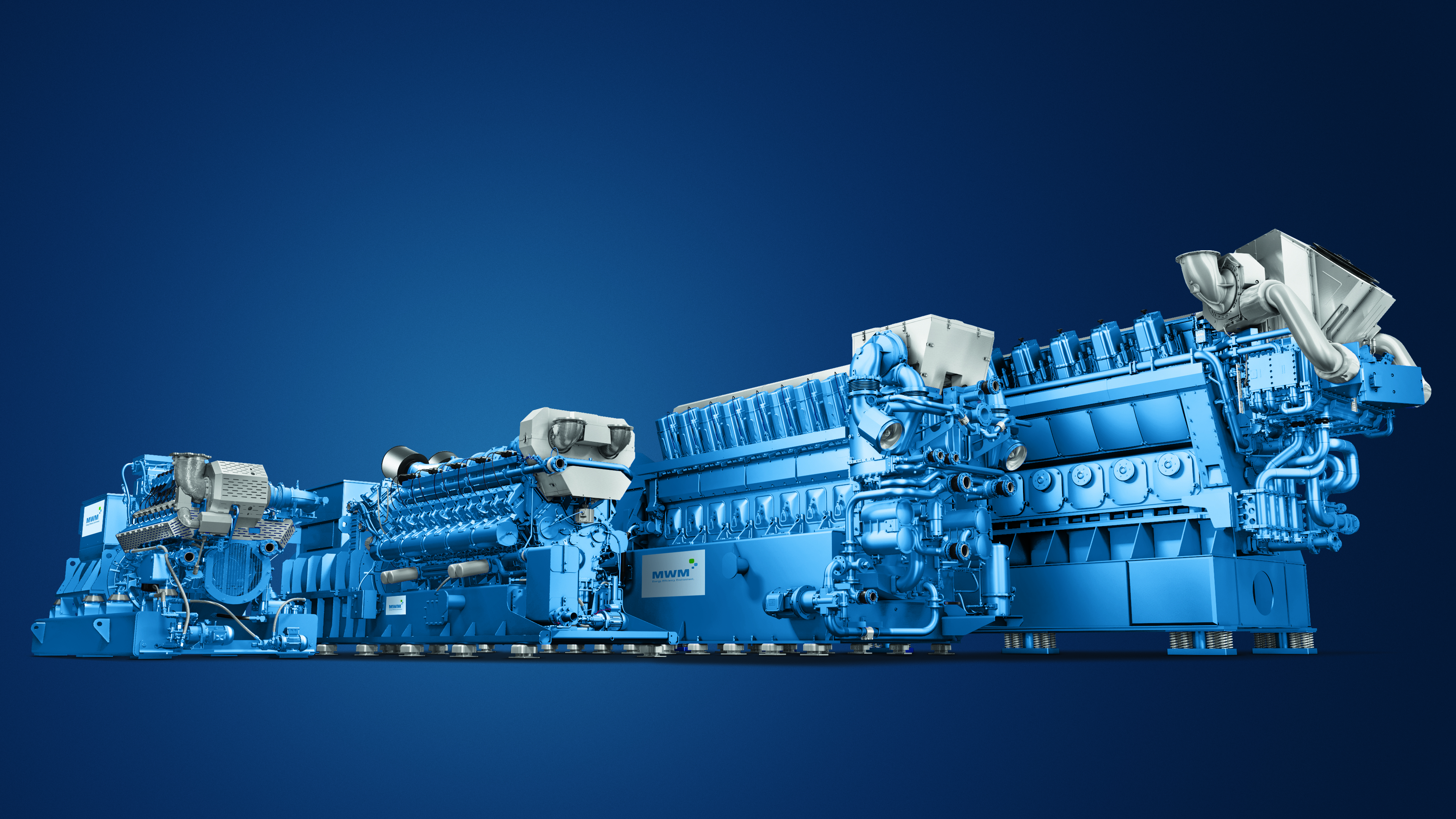
MWM gas engines can be operated with various types of gas, such as natural gas, shale gas, mine gas, biogas, landfill gas, sewage gas, and syngas. They are designed for maximum electrical and thermal efficiency, low operating and service costs, and high reliability and availability. In this way, they reach efficiency levels of more than 90 percent.
Further information:
- Press release: MWM Flex Cogeneration Power Plant for Biogas Plant in Lower Saxony Designated “Cogeneration Power Plant of the Month” of January
- Press release: Sustainable and Highly Efficient: Bausch + Lomb Saves up to €1 Million in Operating Costs and about 3,750 t of Carbon a Year with Newly Installed MWM TCG 2032 Gas Engine
- Press release: CHP Plant with MWM TCG 2016 V16 Gas Engine in Chocolate Factory Honored as Highly Sustainable Energy Concept
- Press release: Energy Security in the Manufacturing and Utilities Industries through Cogeneration and Trigeneration Plants
- MWM Gas Engines and Power Gensets
- MWM Cogeneration Power Plants
Contact Media
Aljoscha Kertesz
Manager Communications
T +49 621 48 18 35 76
E mwm-press@cat.com
Frank Fuhrmann
Online Editor
Member of DPV / German Press Association
T +49 621 48 18 35 16
E mwm-press@cat.com